Energy Efficiency Improvement of Glass Furnace
- Representative Participant
- Ihara Furnace Co., Ltd.
Outline of GHG Mitigation Activity
The introduction of an automatic combustion control system in glass furnaces reduces massive fuel consumptions and thus reduces GHG emissions. The core technology adopted by the project is the computerised combustion system. A glass furnace consumes a lot of fuel because their internal temperature reaches more than 1500 degrees Celsius, and operates 24 hours a day without stopping. The control system monitors air pressure, fuel flow, furnace temperature, oxygen rate, etc., and determines the optimum volume of air intake by automatically adjusting fuel valves and air inlet dampers.
Expected GHG Emission Reductions
3,600tCO2/yr
← Annual glass production of Ralaco: 12.500t-glass
← Specific GHG emission reduction: 0.288tCO2/t-glass
Site of JCM Project
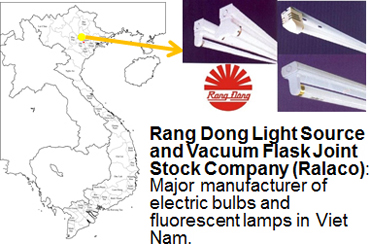